1. Introduction
Medical injection molding, a cornerstone of medical device manufacturing, directly impacts product safety and performance stability. While conventional injection molding has long dominated the field, emerging challenges—such as gas entrapment defects, compromised microstructure formation, and yield losses—have become increasingly pronounced as medical devices evolve toward higher precision and integration. Vacuum injection molding, which actively intervenes in the gas environment, offers an innovative solution to these issues, particularly in applications like implantable devices and advanced diagnostic equipment. This article systematically compares the two processes across four dimensions: process principles, quality control, cost-benefit analysis, and typical application scenarios.
2. Process Principles: A Paradigm Shift in Gas Management
2.1 Passive Gas Exhaust in Conventional Injection Molding
Conventional injection molding relies on passive exhaust structures (e.g., vent slots, porous steel) to release trapped gas during melt filling via mold gaps (0.02–0.04 mm). Key limitations include:
-
Limited Exhaust Efficiency: Complex thin-walled structures (e.g., pacemaker casings) exhibit gas entrapment rates of 12–18%, leading to surface defects like flow marks and silver streaks.
-
Material Compatibility Constraints: Hydrolysis-sensitive materials (e.g., PLA biodegradable resins) are prone to bubble formation due to thermal degradation, failing to meet requirements for biodegradable stents.
-
Narrow Process Windows: Injection speed, packing pressure, and other parameters require extensive tuning, limiting adaptability to multi-variety, low-volume production.
2.2 Active Gas Control in Vacuum Injection Molding
Vacuum injection molding establishes a near-space environment (−0.095 MPa or higher) via vacuum pumps before melt filling, achieving near-zero gas conditions. Technological breakthroughs include:
-
Zonal Dynamic Vacuum Control: Systems like ENGEL viper enable targeted evacuation of deep ribs and microchannels, reducing electrolyte leakage risks in battery separators (e.g., 4680 cells) to below 0.3%.
-
Expanded Material Adaptability: Paired with high-temperature bio-based nylons (e.g., DuPont Zytel® HTN FR52G), it enables 30% weight reduction, aligning with ventilator housing lightweighting demands.
-
Enhanced Process Stability: Modular vacuum sealing systems (e.g., HASCO Vario) reduce mold retrofitting costs by 40%, with integrated 3D-printed conformal cooling channels and vacuum pathways emerging as a trend.
3. Quality Control: From "Functional" to "Zero-Defect" Standards
3.1 Surface Quality and Biocompatibility
-
Vacuum Molding Advantage: VR lens modules demand nanoscale surface roughness (Ra < 0.01 μm). Vacuum processes eliminate gas-induced orange peel textures, meeting endoscopic optical component imaging precision requirements.
-
Conventional Molding Limitations: PVC infusion set tees are prone to micro-voids under conventional injection, leading to cyclohexanone solvent residue exceeding limits and increasing thrombosis risks.
3.2 Structural Integrity and Mechanical Performance
-
Vacuum Molding Breakthrough: Biodegradable cardiovascular stents achieve porosity reduction from 25% to <5% via vacuum molding, mitigating thrombosis risks.
-
Conventional Molding Risks: PEEK spinal fusion cages under conventional injection exhibit delamination, reducing fatigue test lifespan by 40%.
3.3 Process Control and Traceability
-
Vacuum Molding Innovation: Vacuum data integration with MES systems enables piezoresistive sensor calibration every 500 cycles, narrowing process parameter fluctuations to ±0.5%.
-
Conventional Molding Pitfalls: Traditional processes rely on manual inspections, achieving defect detection rates below 80%.
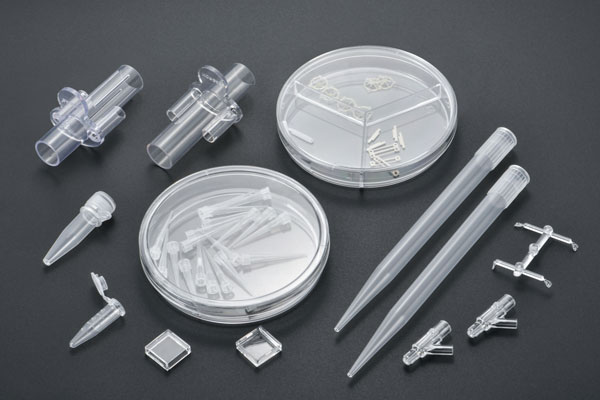
4. Cost-Benefit Analysis: Value Reconfiguration from a Lifecycle Perspective
4.1 Initial Investment and Operating Costs
-
Vacuum Molding Challenge: Equipment costs are 25% higher than conventional molding, but modular vacuum units (e.g., Hasco Vacuum Jet) support incremental upgrades, with single-unit costs as low as ¥30,000.
-
Conventional Molding Traps: Hidden costs from yield losses are underestimated. A Tier 1 supplier reduced per-unit costs by 19% for high-gloss grille components after adopting vacuum processes.
4.2 Material Utilization and Production Efficiency
-
Vacuum Molding Dividends: Bio-based materials exhibit 15–20% improved flowability, shortening injection-molded syringe barrel cycles by 12% and reducing scrap rates from 8% to 1.5%.
-
Conventional Molding Bottlenecks: PP infusion bags require secondary finishing to eliminate flash, increasing labor costs by 30%.
4.3 Regulatory Compliance and ESG Performance
-
Vacuum Molding Advantage: Compliance with ISO 13485:2016 and FDA 21 CFR Part 820. A CT scanner manufacturer reduced the carbon footprint of data acquisition modules by 22% using vacuum processes.
-
Conventional Molding Risks: DEHP plasticizer leaching in PVC dialysis tubing remains a regulatory concern.
5. Typical Application Scenarios and Process Selection Strategies
5.1 High-Risk Implantable Devices
-
Vacuum Molding Mandatory: PEEK artificial joint stems achieve 200 MPa fatigue strength via vacuum molding, meeting 20-year service life requirements.
-
Conventional Molding Prohibited: Titanium-PEEK composite structures require vacuum insert molding to prevent delamination.
5.2 Precision Diagnostic Equipment
-
Vacuum Molding Preferred: Flexible circuit carriers for continuous glucose monitors demand vacuum microcellular molding, maintaining thickness tolerances within ±0.02 mm.
-
Conventional Molding Limitations: PET ultrasound probe casings warp under conventional injection, causing image distortion rates to exceed standards.
5.3 Rapidly Iterated Consumables
-
Conventional Molding Suitable: Disposable syringe barrels achieve color differentiation between graduations and bodies via two-shot injection molding, with mold lifespans exceeding 500,000 cycles.
-
Vacuum Molding Supplementary: Central venous catheter tips embed stainless steel guidewires via vacuum injection, reducing vascular penetration risks.
6. Conclusion
Vacuum injection molding and conventional injection molding are not mutually exclusive in medical device manufacturing but form a complementary technological matrix. While conventional injection molding retains dominance in standardized, high-volume consumables due to cost advantages, vacuum injection molding has emerged as the preferred process for high-precision, high-reliability medical devices by overcoming gas management limitations. Future advancements in 3D-printed molds, intelligent vacuum control, and hybrid processes will drive medical injection molding toward a "process combination" approach. Engineers must tailor solutions based on product lifecycle, ESG goals, and microstructure complexity.