I. Introduction
In the medical field, the selection of materials is of crucial importance, as it directly relates to the safety, effectiveness, and patient experience of medical devices and supplies. Medical PC (polycarbonate) and medical PP (polypropylene) are two commonly used medical plastic materials, each with unique performance characteristics suitable for different medical scenarios. This article will conduct a comparative analysis of the performance of medical PC and medical PP and explore their application scopes, providing references for material selection in the medical industry.
II. Performance Comparison of Medical PC and Medical PP
(1) Physical Properties
-
Density
-
The density of medical PC generally ranges from 1.2 - 1.3g/cm³, which is relatively high.
-
The density of medical PP is usually between 0.9 - 0.91g/cm³, making medical PP products lighter in weight.
-
Strength and Toughness
-
Medical PC has high strength and toughness, with outstanding impact strength. It can maintain good toughness even at low temperatures and is less prone to brittle fracture.
-
Medical PP has moderate strength and good toughness, but its toughness decreases at low temperatures. Compared to medical PC, its impact resistance is slightly weaker.
-
Hardness
-
Medical PC has a relatively high hardness, generally in the range of 80 - 120 on the Shore scale, with a hard surface texture.
-
Medical PP has a relatively low hardness, usually between 60 - 90 on the Shore scale, with a relatively soft surface.
(2) Chemical Properties
-
Chemical Resistance
-
Medical PC has good resistance to common acids, alkalis, and salt solutions but may swell or dissolve in certain organic solvents (such as acetone, benzene, etc.).
-
Medical PP exhibits excellent chemical resistance, with good tolerance to most acids, alkalis, salt solutions, and organic solvents, showing high chemical stability.
-
Aging Resistance
-
Medical PC is prone to aging under ultraviolet radiation, leading to a decline in performance. Therefore, ultraviolet absorbers need to be added to improve its aging resistance.
-
Medical PP has relatively good aging resistance and ages slowly in the natural environment. However, it may also undergo a certain degree of aging when exposed to high temperatures and ultraviolet radiation for a long time.
(3) Processing Properties
-
Molding Processing
-
Medical PC can be processed into various shapes through multiple molding processes such as injection molding, extrusion, and blow molding. Injection - molded products have high dimensional accuracy and good surface quality.
-
Medical PP also has good processing properties, with a short injection - molding cycle and high production efficiency. Moreover, it has a low molding shrinkage rate, ensuring good dimensional stability of the products.
-
Secondary Processing
-
Medical PC can undergo secondary processing such as cutting, drilling, and polishing. Good processing performance is achieved, but attention should be paid to prevent crack generation during processing.
-
Medical PP is also easy to subject to secondary processing, such as welding and heat - sealing, and has high welding strength.
(4) Biocompatibility
-
Medical PC
-
After special modification treatment, medical PC can meet certain biocompatibility standards, such as ISO 10993. It can be used for medical devices in short - term contact with the human body, but generally, its biocompatibility is slightly inferior to that of medical PP.
-
Medical PP
-
Medical PP has good biocompatibility and is widely used in the manufacture of medical devices and supplies in direct contact with the human body, such as syringes and infusion bags. Its safety has been verified over a long time.
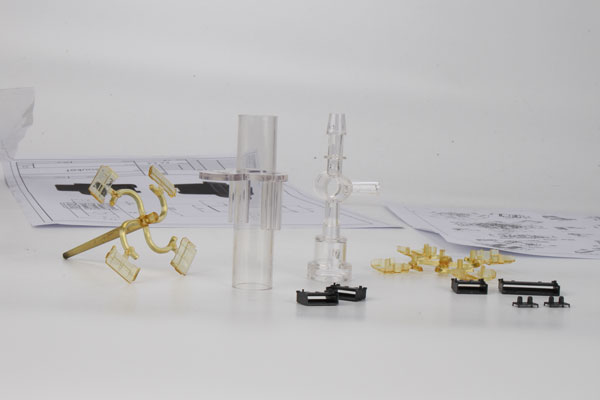
III. Application Scopes of Medical PC and Medical PP
(1) Application Scope of Medical PC
-
Medical Device Shells
-
Due to its high strength, toughness, and good appearance texture, medical PC is often used to manufacture the shells of medical devices, such as monitor shells and ventilator shells, which can ensure the structural strength of the equipment and provide an aesthetically pleasing appearance.
-
Ophthalmic Devices
-
With high transparency and good optical performance, medical PC can be used to manufacture ophthalmic devices, such as intraocular lenses and contact lenses, providing patients with a good visual experience.
-
Disposable Medical Supplies
-
Specially treated medical PC can be used to manufacture some disposable medical supplies, such as the shells of disposable blood collection devices, meeting the requirements of single - use while ensuring performance.
(2) Application Scope of Medical PP
-
Syringes and Infusion Sets
-
Medical PP, with its good biocompatibility, high chemical stability, and low cost, is an ideal material for manufacturing syringes and infusion sets, ensuring the safety and effectiveness of drug storage and delivery.
-
Medical Packaging Materials
-
Medical PP can be used to manufacture medical packaging materials, such as pharmaceutical packaging bottles and reagent bottles. Its good sealing and chemical - resistance properties can protect the quality of drugs and reagents.
-
Surgical Instrument Trays
-
Due to its low density and light weight, medical PP is easy to carry and clean. It is often used to manufacture surgical instrument trays, facilitating the access of medical staff to instruments during surgery.
IV. Selection Suggestions
When choosing between medical PC and medical PP, the following factors need to be comprehensively considered:
-
Product Performance Requirements: If high requirements are placed on the strength, toughness, and transparency of the product, medical PC can be selected; if more attention is paid to biocompatibility, chemical stability, and cost, medical PP may be a better choice.
-
Usage Scenario: According to the usage scenario of the medical device or supply, such as whether it is in direct contact with the human body or whether it needs to be exposed to a harsh environment for a long time, an appropriate material should be selected.
-
Budget Constraints: Medical PC is relatively expensive, while medical PP has a lower cost. Within the premise of meeting performance requirements, the choice can be made based on the budget.
V. Conclusion
Medical PC and medical PP, as two important medical plastic materials, each have unique performance characteristics and application scopes. Medical PC, with its high strength, toughness, and good optical performance, plays an important role in the fields of medical device shells and ophthalmic devices. Medical PP, with its excellent biocompatibility, chemical stability, and low - cost advantages, is widely used in syringes, infusion sets, and medical packaging materials. In practical applications, medical PC or medical PP should be reasonably selected based on specific product requirements, usage scenarios, and budget factors to ensure the quality and safety of medical devices and supplies. Meanwhile, with the continuous development of materials science, the performance of medical PC and medical PP will continue to improve, providing more possibilities for the development of the medical industry.
Dongguan Yize Mould specializes in the design and manufacture of precision molds and the production of precision injection - molded products in the medical field. With rich experience in the application of medical materials and a professional technical team, we can provide customers with one - stop solutions from material selection, product design to injection molding and assembly. If you have relevant needs, please feel free to contact us at +86 13302615729.