Medical Injection Molding: Hot Runner vs. Cold Runner
DATE:2025-04-28 HITS:305
I. Specialized Requirements in Medical Injection Molding
-
Material Sensitivity
-
Medical-grade polymers (e.g., PPSU, COC, medical silicone) cost 3–5 times higher than engineering plastics, demanding >99% material utilization.
-
Heat-sensitive materials (e.g., flame-retardant PBT) risk molecular degradation under prolonged thermal stress.
-
Cleanliness & Regulatory Compliance
-
Residues in runners pose microbial contamination risks, requiring FDA 21 CFR Part 177 and USP Class VI compliance.
-
Volatile substance migration (e.g., PVC plasticizers) must be minimized; cold runner residues exacerbate this risk.
-
Process Stability
-
Tolerance demands (±0.02mm) for critical components (e.g., microfluidic chips) necessitate balanced melt flow via runner design.
-
Sterilization compatibility (ETO/γ-ray/autoclave) requires corrosion-resistant runner materials (e.g., 316L stainless steel liners).
II. Technical Comparison: Hot Runner vs. Cold Runner
1. Medical-Grade Hot Runner Systems
-
Advantages
-
Zero Waste: 99.5% material utilization saves >$150k/year (e.g., PPSU catheter production).
-
Consistency: ±1°C temperature control reduces manual intervention, aligning with GMP standards.
-
High Efficiency: 30% cycle time reduction boosts daily output by 40% (e.g., ventilator components).
-
Challenges
-
Cleaning Complexity: CIP systems required to prevent cross-contamination, adding 15–20% maintenance costs.
-
Material Limits: Fluoropolymers (e.g., PTFE) corrode standard nozzles, necessitating tungsten-coated nozzles (+30% cost).
2. Medical Cold Runner Systems
-
Advantages
-
Design Flexibility: Supports multi-cavity molds (e.g., 128-cavity viral transport tube caps) with shorter lead times.
-
Low Maintenance: No temperature control reduces maintenance costs by 40%, ideal for disposable devices (e.g., swab sticks).
-
Material Compatibility: Suitable for heat-sensitive polymers (e.g., anticoagulant-containing PETG).
-
Drawbacks
-
Waste Handling: 15–20% runner scrap requires closed-loop recycling systems, increasing costs by 8–12%.
-
Quality Variability: Weld lines at runner ends compromise mechanical strength (e.g., syringe plunger breakage risk).
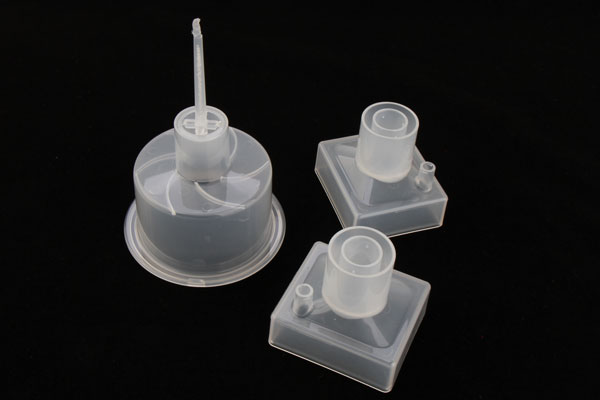
III. Decision-Making Framework for Medical Applications
Dimension
|
Hot Runner Priority Scenarios
|
Cold Runner Priority Scenarios
|
Product Type
|
Implantables (e.g., orthopedic screws), precision catheters
|
Disposables (e.g., face mask nose wires), low-value consumables
|
Annual Volume
|
≥500k units (ROI <18 months)
|
<200k units (lower tooling amortization)
|
Sterilization
|
ETO/γ-ray compatible (no thermal stress residues)
|
Autoclave-friendly (easier runner cleaning)
|
Regulatory Needs
|
FDA DMF for runner materials
|
ISO 80369-1 compliance for small-bore connectors
|
IV. Case Studies in Medical Applications
-
Hot Runner Success Story
-
Product: Cardiac stent delivery microcatheter (0.15mm wall thickness)
-
Solution: Valve-gated hot nozzle + ceramic heater, reducing pressure fluctuation to <0.5bar.
-
Outcome: Defect rate reduced from 18% to 2%, annual capacity reached 2M units (MDR-certified).
-
Cold Runner Innovation
-
Product: 96-well PCR plate (cross-contamination prevention)
-
Solution: Multi-stage cold runner + automated sprue cutting, achieving 100% automatic detachment.
-
Outcome: Daily output of 50k units met urgent COVID-19 test kit demands.
V. Technology Upgrades & Compliance Strategies
-
Smart Medical Injection Molding
-
AI vision systems for real-time melt monitoring (99.9% defect detection accuracy).
-
3D-printed runner liners (SLM 316L stainless steel) cut tooling lead times by 50%.
-
Hybrid Runner Systems
-
Hot runner for main channel (pressure loss reduction) + cold runner with sub-gate for automated sprue separation.
-
Example: Insulin pen injector components achieved 97% material utilization and 25% cycle time reduction.
-
Compliance Enhancements
-
Cleaning Validation (CCV) with ATP bioluminescence testing (<1 CFU/cm² residue limit).
-
Mold traceability via QR codes (recording heat treatment parameters and usage cycles).