In the sophisticated system of a life detector, the shell serves as a crucial component that protects the internal precision electronic components and ensures the stable operation of the device in various complex environments. It needs to possess good mechanical strength, corrosion resistance, electromagnetic shielding performance, and an appropriate appearance and texture. Injection molding, with its characteristics of high efficiency, precision, and the ability to form complex structures, has become an ideal process for manufacturing life detector shells. This article will delve into the component forming methods, innovative material applications, and relevant technical points in the injection molding processing of life detector shells.
I. Polycarbonate (PC) Shell: The Perfect Combination of High Strength and Transparency
-
Material Characteristics
Polycarbonate (PC) is well - known for its excellent impact resistance, high transparency, and good heat resistance. In the application of life detector shells, PC material can withstand a certain degree of external impact, protecting the internal components from damage. Meanwhile, its high transparency facilitates operators to observe the operating status of device indicators. According to relevant research, the impact resistance of PC is 200 - 300 times that of ordinary glass, and its performance remains stable within the temperature range of - 40℃ to 130℃.
-
Injection Molding Process
PC shells are usually manufactured using the injection molding process. During the injection molding process, precisely controlling parameters such as the injection temperature, injection pressure, and holding time is crucial. For example, a professional life detector manufacturer optimized the injection molding parameters and increased the impact resistance of PC shells by 20%, while reducing defects such as weld lines on the product surface, thus improving the overall quality of the product.
II. Acrylonitrile - Butadiene - Styrene Copolymer (ABS) Shell: A Balanced Choice of Cost and Performance
-
Material Characteristics
ABS material has good toughness, hardness, and processability, and its price is relatively affordable. It has certain chemical resistance and surface gloss, which can meet the usage requirements of life detector shells in general environments. Literature points out that ABS material is widely used in fields such as electrical appliance shells, making it a highly cost - effective choice.
-
Innovation in Injection Molding
To improve the electromagnetic shielding performance of ABS shells, researchers added conductive fillers such as carbon black or metal fibers to the ABS matrix, achieving the conductive treatment of ABS shells. This innovative process not only retains the original advantages of ABS material but also endows the shell with good electromagnetic shielding ability, effectively preventing external electromagnetic interference from affecting the normal operation of the device. After adopting this process, a technology company increased the stability of the life detector in complex electromagnetic environments by 30%.
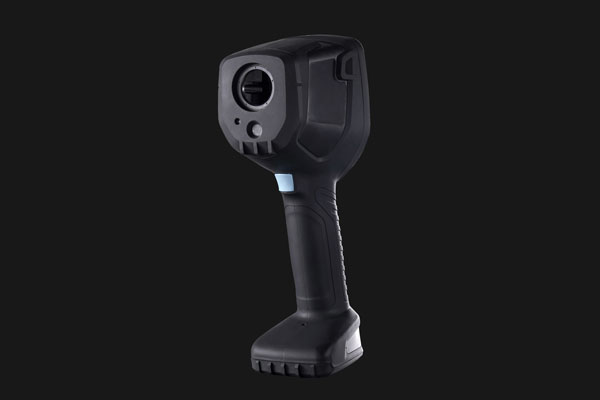
III. Nylon (PA) Shell: Excellent Performance in Wear Resistance and Self - Lubrication
-
Material Characteristics
Nylon material has excellent wear resistance, self - lubrication, and fatigue resistance. In the harsh working environments that a life detector may face, such as dusty, humid, or frictional scenarios, a nylon shell can maintain good performance and extend the service life of the device. According to literature, the wear resistance of nylon has led to its wide application in many industrial fields.
-
Exploration of Injection Molding
To address the problem of internal stress easily generated in nylon material during the injection molding process, researchers have developed a new injection molding process. By optimizing mold design and injection molding parameters, and adopting multi - stage injection and slow cooling methods, the internal stress of nylon shells has been effectively reduced, and the dimensional stability and deformation resistance of the products have been improved. After applying this process, a company reduced the rejection rate of nylon shells by 40%, significantly improving product quality.
IV. Liquid Crystal Polymer (LCP) Shell: A Model of High Performance and Lightweight
-
Material Characteristics
Liquid crystal polymer (LCP) has high strength, high modulus, low moisture absorption, and excellent dimensional stability. Its unique molecular structure endows the material with outstanding mechanical properties and thermal stability, while its low density is conducive to the lightweight design of life detectors. Literature shows that LCP is increasingly widely used in high - end fields such as aerospace and electronic appliances.
-
Innovation in Injection Molding
The injection molding of LCP shells requires precise control of temperature and pressure to avoid material degradation. By using advanced injection molding equipment and optimized process parameters, high - precision molding of LCP shells has been achieved. For example, a high - end electronic equipment manufacturer successfully manufactured an LCP shell with uniform wall thickness and a dimensional accuracy of ±0.05mm by using a special screw design and mold temperature control system, meeting the demand for high - performance shells for life detectors.
V. Composite Material Shell: A Multifunctional and Customized Solution
-
Material Characteristics
Composite materials, such as carbon fiber reinforced plastic (CFRP) and glass fiber reinforced plastic (GFRP), combine the advantages of different materials, with functions such as high strength, low density, corrosion resistance, and electromagnetic shielding. The composition and performance of composite materials can be customized according to the specific usage requirements of life detectors to achieve the multifunctionality of the shell. According to research, composite materials show great potential in the shell applications of high - end electronic devices.
-
Injection Molding Technology
The injection molding of composite material shells faces many challenges, such as the uniform dispersion of fibers and the control of material fluidity. By developing new composite material formulations and injection molding processes, such as using prepreg technology and special screw combinations, high - quality injection molding of composite material shells has been achieved. An innovative company successfully developed a composite material shell with high strength, high electromagnetic shielding performance, and lightweight characteristics using this technology, providing strong support for the performance improvement of life detectors.
VI. Summary
Injection molding plays an irreplaceable and important role in the manufacturing of life detector shells. The injection molding technologies of different materials provide broad space for improving shell performance and expanding functions. Through continuous technological innovation and process optimization, not only can the production efficiency and product quality of shells be improved, but also the diverse needs of life detectors in different application scenarios can be met. In the future, with the continuous development of material science and injection molding technology, injection molding is expected to create more possibilities in the field of life detector shell manufacturing and provide more solid guarantees for the development of life detection technology.