Medical injection molding products, due to their direct or indirect contact with the human body, must meet stringent requirements for safety, precision, and stability. From surgical instruments to implants, diagnostic device housings to microfluidic chips, every step in the injection molding process impacts patient health and product compliance. This article systematically outlines core considerations across four dimensions—material selection, mold design, process parameters, and quality control—to help enterprises mitigate risks and produce high-quality medical products.
1. Material Selection: Compliance and Biocompatibility Are Non-Negotiable
Medical injection molding materials must meet three critical standards:
-
Regulatory Certification: Prioritize medical-grade materials with FDA (U.S.), CE (EU), or CFDA (China) approval, such as polypropylene (PP), polyethylene (PE), polycarbonate (PC), and polyether ether ketone (PEEK). Avoid industrial-grade or recycled materials to prevent harmful substance migration.
-
Biocompatibility: Select materials based on contact type (e.g., skin, mucosa, implantation). Implantable materials must pass ISO 10993 tests for cytotoxicity, sensitization, and genotoxicity.
-
Performance Alignment: Evaluate transparency, chemical resistance, impact strength, and sterilization compatibility (e.g., 121°C steam sterilization). For example, syringes require high transparency and low friction, while surgical tool handles need anti-slip durability.
Case Warning: A company faced lawsuits and reputational damage after using uncertified materials for IV sets, causing allergic reactions in patients.
2. Mold Design: Balancing Precision and Cleanliness
Medical molds demand innovations beyond conventional manufacturing:
-
Microstructure Molding: High-precision CNC or EDM machining is essential for features like micro-holes, threads, and thin walls (e.g., microfluidic channels), with tolerances controlled within ±0.005mm.
-
Ejection and Venting Optimization: Slide mechanisms and vent slots must prevent surface scratches and trapped air, which can cause burns or silver streaking.
-
Cleanliness Assurance: Mirror-finish polishing (Ra ≤ 0.05μm) reduces surface defects, while corrosion-resistant steel (e.g., S136H) avoids metal contamination.
Emerging Trend: 3D-printed molds are gaining traction for rapid prototyping and low-volume medical production, cutting development time by 40%.
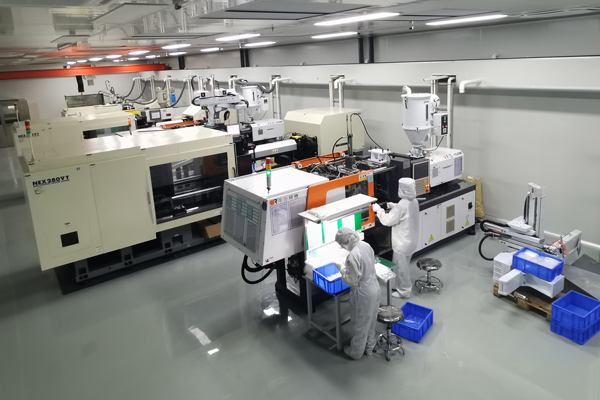
3. Process Parameters: Dynamic Control for Stable Mass Production
Medical molding requires unwavering process stability:
-
Temperature Management:
-
Barrel Temperature: Adjust based on material flow (e.g., 280–320°C for PC vs. 200–240°C for PP).
-
Mold Temperature: Precision control (±1°C) affects crystallinity and shrinkage. Low-temperature molds (40–60°C) minimize internal stress for high-precision gears.
-
Injection Speed and Pressure: Multi-stage injection programs optimize filling (high speed to avoid cold material, low pressure to reduce stress). Backpressure (5–15 bar) balances material degradation and color mixing.
-
Sterilization Compatibility: Account for shrinkage allowances if products undergo post-molding sterilization (e.g., EO sterilization may increase PP shrinkage by 0.2–0.5%).
Data Insight: A medical enterprise reduced defect rates from 3.2% to 0.5% by optimizing injection speed curves, saving over $2 million annually.
4. Quality Control: End-to-End Traceability and Risk Prevention
Quality assurance must span R&D, production, and testing:
-
Cleanroom Standards: Maintain ISO 14644-1 Class 7 or higher environments to control particles (≥0.5μm particles ≤ 352,000/m³).
-
In-Line Inspection: Machine vision systems detect defects like flash, short shots, and black spots with 0.01mm accuracy. Laser thickness gauges ensure critical dimensions meet specifications.
-
Batch Traceability: Implement MES systems to record parameters, test data, and operator details for each batch, complying with FDA 21 CFR Part 11 electronic records requirements.
Industry Benchmark: A global medical firm cut recall rates by 70% using real-time MES alerts and full traceability.
Conclusion: Craftsmanship for Patient Safety
Medical injection molding merges technology, regulation, and responsibility. Enterprises must adopt a “prevention-first” culture, optimizing material selection, mold maintenance, and staff training to build risk-proof supply chains. Only then can they safeguard patients while earning market trust.
Discussion Topic: What challenges have you faced in medical injection molding? Share your experiences in the comments to explore solutions together!