In the field of medical device manufacturing, injection molding stands as a core production method due to its high efficiency and precision. From surgical instruments to implantable devices, from diagnostic equipment to medical consumables, the quality of injection-molded parts directly impacts patients' lives. However, the unique nature of medical injection molding demands that the production process transcend the limitations of traditional manufacturing, establishing stringent standards in material selection, process control, environmental management, and other areas. This article provides an in-depth analysis of six core considerations in the medical injection molding process, offering systematic guidance for industry practitioners.
1. Material Selection: Biocompatibility as the Top Priority
Medical injection molding materials must meet dual standards: possessing the mechanical properties of engineering plastics while also passing biocompatibility certifications. Take polycarbonate (PC) as an example. Its high transparency and impact resistance make it suitable for manufacturing infusion sets and pulse oximeter housings. However, only medical-grade raw materials that comply with ISO 10993 standards must be used to ensure no cytotoxicity or allergenic reactions. For catheters and sheaths that directly contact blood, inert materials like polyether ether ketone (PEEK) or ultra-high-molecular-weight polyethylene (UHMWPE) are required to prevent protein adsorption and thrombus formation.
Key Control Points:
-
Supplier qualification review: Require the provision of FDA 510(k) certification, CE marking, and complete biocompatibility test reports.
-
Batch consistency management: Each batch of materials must undergo testing for parameters such as melt flow rate and shrinkage, with fluctuations controlled within ±5%.
-
Pre-treatment processes: PC materials need to be dried at 120-130°C for 3-4 hours to reduce moisture content to below 0.02%, preventing hydrolysis-induced strength degradation.
2. Mold Design: Achieving the Perfect Balance Between Precision and Functionality
The manufacturing precision of medical injection molds must reach the micrometer level. For instance, the wall thickness tolerance of a pacemaker housing must be controlled within ±0.005mm. Mold design should incorporate the following elements:
-
Cooling system optimization: Adopt conformal cooling channel designs to improve mold temperature uniformity by 40%, reducing deformation caused by thermal stress.
-
Venting structure innovation: Install vacuum venting slots in micro-structured areas to prevent gas entrapment and bubble defects.
-
Insert integration technology: For metal-plastic composite parts, design pre-compression structures to ensure the bonding strength between inserts and plastics. For example, the interference fit between the metal needle and plastic sheath of a vascular sheath must be precisely controlled to 0.01mm.
Typical Case: A company's mold for minimally invasive surgical forceps achieved a mold life increase from 300,000 cycles to 1 million cycles by adopting nano-coating technology, while reducing product burr height to below 0.003mm.
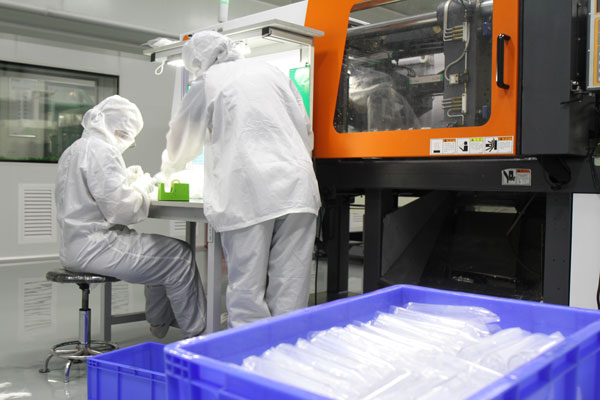
3. Process Control: Precise Regulation of the Parameter Matrix
Medical injection molding requires the establishment of a dynamic process parameter database. Taking PC material for manufacturing rigid oxygen masks as an example, the typical process window is as follows:
-
Barrel temperature: 280-320°C (segmented control, with the nozzle temperature 5-10°C lower)
-
Injection speed: Multi-stage injection, with the initial speed at 80mm/s and the final speed reduced to 20mm/s
-
Holding pressure: Three-stage decreasing pressure, from 80MPa gradually reduced to 30MPa
-
Cooling time: Dynamically adjusted according to product wall thickness, ensuring mold cavity pressure drops below 0.5MPa before mold opening
Special Process Requirements:
-
Annealing treatment: Perform annealing at 50-60°C for 1-2 hours on high-stress products to eliminate internal stress.
-
Dynamic holding pressure: Use servo valves to control holding pressure with 0.1MPa precision.
-
Process monitoring: Deploy infrared temperature measurement systems and mold cavity pressure sensors to collect over 200 process parameters in real-time.
4. Clean Production: Comprehensive Control of the Sterile Environment
Medical injection molding workshops must meet ISO Class 7 (10,000-class) cleanliness standards, with key control measures including:
-
Airflow organization design: Adopt vertical unidirectional flow with an air exchange rate of ≥50 times per hour, ensuring a suspended particle concentration of ≤352,000 particles/m³ (≥0.5μm).
-
Personnel control: Operators must wear cleanroom suits, pass through air showers for dust removal, and wear nitrile gloves after hand disinfection before working.
-
Equipment protection: Injection molding machines should feature fully enclosed structures equipped with HEPA filtration systems to prevent oil mist contamination.
-
Mold maintenance: Perform laser cleaning on molds before each production run to remove particles larger than 0.1μm, with post-cleaning verification via ATP bioluminescence testing.
Data Support: After implementing clean production upgrades, one company reduced product microbial contamination rates from 0.3% to 0.005% and decreased defect rates by 62%.
5. Quality Inspection: Multi-Dimensional Failure Mode Analysis
Medical injection-molded parts must pass a "five-dimensional inspection system":
-
Dimensional inspection: Use coordinate measuring machines (CMMs) for full-dimensional scanning, with a dimensional compliance rate of 99.97%.
-
Performance testing:
-
Tensile strength: ≥50MPa (ASTM D638)
-
Impact toughness: ≥20kJ/m² (ISO 179)
-
Chemical resistance: No discoloration or cracking after 72-hour immersion in 75% ethanol solution
-
Biological testing:
-
Cytotoxicity test (ISO 10993-5): Cell viability ≥80%
-
Hemolysis rate test (ISO 10993-4): Hemolysis rate ≤5%
-
Cleanliness testing: Use liquid chromatography-mass spectrometry to detect extractable metal content ≤0.1μg/g.
-
Reliability verification: Conduct 100,000-cycle fatigue testing to ensure no failure under cyclic loading.
6. Compliance Management: Seamless Integration of Global Standards
Medical injection molding companies must establish a "three-tier compliance system":
-
Foundational standards: Comply with ISO 13485 quality management system requirements and establish a traceability chain from raw materials to finished products.
-
Regional certifications:
-
EU: Obtain CE certification and meet MDR regulatory requirements.
-
US: Pass FDA 510(k) or PMA approval.
-
China: Obtain NMPA medical device registration certificates.
-
Risk management: Build an FMEA analysis model in accordance with ISO 14971 standards to quantitatively assess 127 potential failure modes.
Industry Trend: With the development of smart healthcare, injection molding technology is integrating with 3D printing and micro/nano manufacturing. One company's microfluidic chip injection molding technology has achieved precise manufacturing with channel dimensions of 50μm and an aspect ratio of 10:1, providing key components for point-of-care testing (POCT) devices.
Medical injection molding represents the perfect fusion of science and art, with its core lying in integrating engineering precision with biological safety. From material selection to finished product delivery, every step demands adherence to a "zero-defect" philosophy, constructing quality firewalls through digital and intelligent means. In today's era of escalating healthcare demands, only by approaching each production detail with reverence can we forge medical quality worthy of trust.