In the realm of medical device manufacturing, precision medical injection-molded components have emerged as an indispensable force driving advancements in modern medical technology. From disposable syringes to implantable artificial joints, and from minimally invasive surgical instruments to in vitro diagnostic equipment, precision injection molding technology is reshaping the medical industry chain with its irreplaceable role. This article explores its core advantages from three dimensions: technical characteristics, clinical value, and industrial efficiency.
1. Micron-Level Precision: Redefining Reliability Standards in Medical Devices
-
Micron-Grade Manufacturing Capability: Precision injection molds utilize high-precision CNC machining and electrical discharge machining (EDM) to achieve dimensional tolerances of ±0.005 mm. For instance, the housing of a pacemaker requires wall thickness uniformity within 0.1 mm, where any minor deviation could lead to electronic component failure. Precision injection molding optimizes mold runner design and injection parameters to ensure each product meets ISO 13485 standards for dimensional stability.
-
Integrated Forming of Complex Structures: Miniature devices like neural electrode catheters require integrated multi-channel fluid pathways and conductive circuits. Traditional manufacturing involves multi-step assembly, whereas precision injection molding achieves single-piece production via multi-cavity molds, reducing assembly errors from 0.2 mm to 0.02 mm. A global enterprise’s diabetes monitoring sensor core component, for example, integrates 12 independent functional modules into one precision-molded part, reducing volume by 60% while tripling reliability.
-
Surface Quality Breakthrough: The surface roughness of medical implants directly impacts tissue compatibility. Precision injection molding employs vacuum coating and laser polishing to achieve a surface roughness of Ra 0.01 μm for titanium alloy artificial joints—80% smoother than traditionally machined products. This ultra-smooth surface reduces bone cement usage and accelerates post-surgical bone integration.
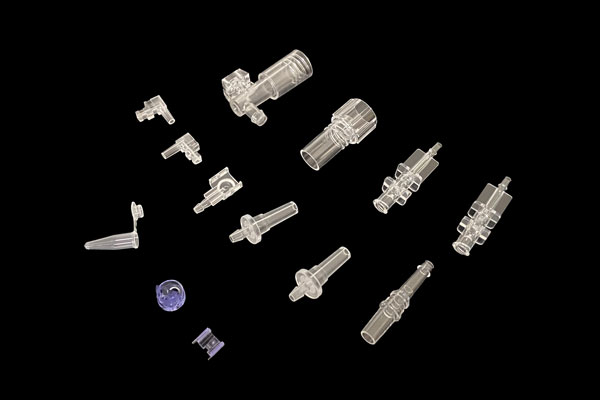
2. Clinical Value Upgrade: From Functional Realization to Experience Optimization
-
Biocompatibility Breakthrough: The application of medical-grade polyetheretherketone (PEEK) and other specialty engineering plastics enables injection-molded components to match the mechanical strength of metals while offering X-ray transparency. A precision-molded spinal fusion cage with 60–80% porosity promotes bone cell ingrowth and reduces stress shielding, increasing post-surgical fusion rates from 75% to 92%.
-
Infection Risk Control: Precision molds polished to a mirror finish (Ra < 0.05 μm) minimize bacterial adhesion areas. Experiments show a 99.6% reduction in bacterial residue on precision-molded surfaces compared to traditional products. A manufacturer of infusion sets reduced catheter-related bloodstream infections from 0.8% to 0.03% by adopting nanoscale surface treatment.
-
Ergonomic Innovation: CAE simulation optimizes wall thickness distribution, enabling lightweighting of irregular structures. A minimally invasive surgical clamp reduced its weight from 120 g to 45 g while maintaining 30 N clamping force, cutting operator fatigue by 65%. Flexible TPE materials in wearable medical devices, precision-molded to a skin contact pressure of 3 kPa (down from 15 kPa), significantly improve patient compliance.
3. Industrial Efficiency Revolution: Reconstructing the Medical Manufacturing Ecosystem
-
Cost Structure Optimization: Precision molds with lifespans exceeding 1 million cycles reduce per-unit mold costs by 70% compared to traditional methods. A hemodialyzer manufacturer cut product defect rates from 5% to 0.3% through mold optimization, saving over RMB 20 million annually. Multi-cavity molds enable production of 8–32 parts per injection, boosting equipment utilization to 92%.
-
Agile Manufacturing: The integration of digital mold design and 3D printing slashes new product development cycles from 18 months to 4 months. During the COVID-19 pandemic, a ventilator component supplier achieved mass production of new face mask sizes within 72 hours using rapid mold-changing systems, quintupling responsiveness to sudden demand.
-
Material Innovation: Nanocomposites enable injection-molded components to combine high strength with transparency. An endoscope lens bracket made of carbon fiber-reinforced PEEK maintains 0.5 mm wall thickness while achieving 150 MPa flexural strength—60% lighter than aluminum alternatives. Shape-memory polymers molded via precision injection molding pave the way for biodegradable stents and other smart medical devices.
4. Future Trends: Intelligent Injection Molding Leads Medical 4.0
With Industry 4.0 penetration, precision medical injection molding is evolving toward intelligence and personalization. An AI-driven injection system developed by a leading enterprise monitors 1,200 process parameters in real time, elevating product consistency to 99.997%. The integration of 3D-printed molds with precision injection molding reduces customized implant production costs by 80% and cuts delivery times to 72 hours.
Under dual pressures of escalating medical demands and cost control, precision medical injection-molded components have become a bridge connecting technological innovation with clinical value. From micron-level precision control to intelligent manufacturing transformations, this technology continues to propel the medical industry toward safer, more efficient, and patient-centric solutions. As material science and digital manufacturing deepen their synergy, precision injection molding will unlock greater potential in personalized medicine, minimally invasive surgery, and other cutting-edge fields.