In the medical industry, a catheter insert with a diameter of only 0.5 mm needs to withstand the pressure of human blood vessels, and a surgical instrument handle requires a dimensional accuracy of 0.01 mm. Behind these stringent requirements lies the in-depth support of precision injection mold processing technology. Taking the mold manufacturing of a medical-grade PC plastic catheter connector as an example, this article systematically analyzes the key technical points throughout the entire process from design to mass production.
I. DFM Stage: The Manufacturability Revolution in Medical Products
1. Product Structure Risk Assessment
Use Moldflow simulation software to conduct 3D modeling of the flow channel system of the catheter connector, focusing on analyzing:
-
The strength of the weld lines at areas with sudden changes in wall thickness (medical products require a strength of ≥ 35 MPa)
-
The filling pressure for a 0.3 mm micro-hole (needs to be controlled between 80 - 120 MPa)
-
The matching degree of the thermal expansion coefficients between the insert and the plastic (the difference in the coefficient of thermal expansion (CTE) between a stainless-steel insert and PC plastic should be < 2 × 10⁻⁵/℃)
2. Material Compatibility Verification
For medical-grade PC plastic (such as Bayer Makrolon 2458), the following tests are required:
-
120℃/4-hour thermal aging test to verify dimensional stability
-
Biocompatibility test (ISO 10993-1 standard)
-
Bonding strength test after knurling treatment of the insert (the pull-out force should be ≥ 50 N)
II. Mold Design: The Engineering Art of Millimeter-Level Precision
1. Core Structure Design
-
Parting Surface Optimization: Adopt a curved parting surface design to hide the parting line on non-functional surfaces.
-
Gate System: Use a combination of a pin gate and a hot runner, with a gate diameter of 0.8 mm and a runner diameter ratio of 1:3.
-
Cooling System: Adopt a conformal cooling channel design, maintaining a distance of 2.5 mm between the cooling channel and the cavity wall, with a flow rate of ≥ 8 L/min.
2. Insert Positioning Innovation
Develop a magnetic positioning device to achieve:
-
A repeatable positioning accuracy of the insert of ± 0.005 mm
-
A clamping time reduced to 8 seconds per piece
-
Prevention of insert displacement caused by injection pressure (displacement < 0.01 mm)
III. Manufacturing: The Path to Nanometer-Level Precision
1. Five-Axis Linked Machining
Use a DMG MORI DMU 50 machine tool for:
-
Cavity rough machining: Leave a margin of 0.15 mm, with a surface roughness of Ra3.2
-
Finish machining: Use a diamond-coated ball-end milling cutter, with a feed rate of 0.05 mm/r and a spindle speed of 18,000 rpm
-
Maintain a sidewall perpendicularity of 0.003 mm/50 mm
2. Electrical Discharge Machining Breakthrough
Apply a Japanese SODICK AQ550L machine tool:
-
Micro-hole machining: With a diameter of 0.3 mm and a depth-to-diameter ratio of 10:1, and a surface roughness of Ra0.8
-
Discharge parameters: Peak current of 3 A, pulse width of 2 μs, and a machining speed of 15 mm³/min
-
Use a multi-electrode replacement process to ensure dimensional consistency of ± 0.002 mm
3. Heat Treatment Process Innovation
Adopt vacuum quenching + cryogenic treatment:
-
Quenching temperature: 850℃, holding for 2 hours
-
Cryogenic treatment: -196℃ × 24 hours to eliminate retained austenite
-
Achieve a final hardness of HRC52 - 54 and improve wear resistance by 300%
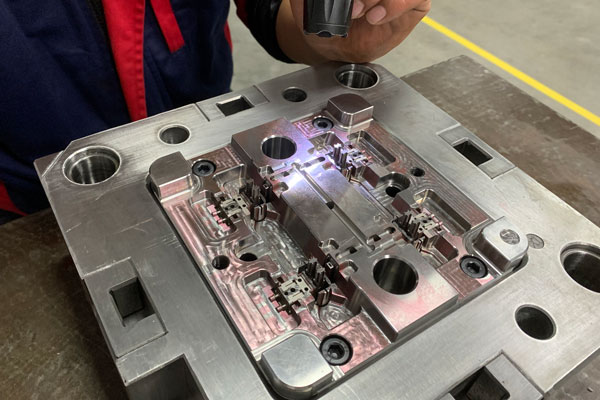
IV. Surface Treatment: The Ultimate Guarantee of Medical-Grade Quality
1. Polishing Process
Use a German PROXXON polishing machine:
-
Rough polishing: Use 800-grit sandpaper to remove machining marks
-
Finish polishing: Use a wool wheel + diamond paste, with a surface roughness of Ra0.025
-
Optical inspection: No scratches or orange peel phenomena
2. Etching Treatment
Apply laser etching technology:
-
Marking clarity: Legible fonts with a size of 0.1 mm
-
Corrosion resistance: Pass a 48-hour salt spray test
-
Biological safety: Comply with the ISO 10993-5 cytotoxicity test
V. Mold Trial and Optimization: Lean Manufacturing Driven by Data
1. Mold Trial Parameter Control
-
Barrel temperature: 290 - 310℃ (segmented control, with the highest temperature at the nozzle)
-
Injection pressure: 120 - 150 MPa (holding pressure is 80% of the injection pressure)
-
Cooling time: 15 - 20 seconds (adjusted in real-time according to the mold temperature)
2. Quality Inspection System
-
Coordinate Measuring Machine (CMM) inspection: Ensure a CPK value of ≥ 1.67 for key dimensions
-
Micro-CT inspection: Detect internal defects with a size of < 0.05 mm
-
Mechanical property testing: Tensile strength ≥ 65 MPa, flexural modulus ≥ 2400 MPa
VI. Mass Production Management: Continuous Guarantee of Medical-Grade Production
1. Mold Maintenance System
-
Daily maintenance: Clean the cavity and lubricate the guide posts
-
Weekly maintenance: Check the wear of the ejector pins and the blockage of the cooling channels
-
Monthly overhaul: Replace wearing parts and conduct mold flow analysis optimization
2. Process Control System
-
Statistical Process Control (SPC) monitoring: Real-time collection of key dimensions and dynamic display of CPK values
-
Error-proofing design: Use sensors to detect whether the insert is in place
-
Traceability system: Bind 15 data items such as mold cavity number and production time for each product
VII. Technical Breakthrough Case: Mold for Minimally Invasive Surgical Instrument Handle
A multinational medical enterprise commissioned the processing of a mold for a laparoscopic handle. The following innovations were made to achieve breakthroughs:
-
Two-Color Injection Molding Technology: Use an ARBURG 630S two-color machine to achieve seamless combination of hard plastic (PC) and soft plastic (TPE).
-
Microcellular Foaming Process: Apply the Mucell technology to form 0.02 mm micro-pores on non-functional surfaces, reducing weight by 15% while maintaining strength.
-
Nano Coating: Use a Parylene coating to reduce the surface friction coefficient to 0.05 and improve operational comfort.
The mold finally achieved:
-
A mold life of over 2 million injection cycles
-
A product defect rate of < 50 ppm
-
A mold delivery cycle shortened to 45 days (compared to the industry average of 75 days)
VIII. Future Trends: The Medical Revolution of Intelligent Injection Molding
-
AI-Optimized Design: Analyze 100,000 sets of mold data through deep learning to automatically generate the optimal gate position.
-
Digital Twin Technology: Establish a virtual mold model to predict the wear state after 500 hours of operation.
-
Additive Manufacturing Breakthrough: Use metal 3D printing to manufacture conformal cooling channels, improving cooling efficiency by 40%.
In the medical industry, precision injection molds have evolved from simple manufacturing tools into core elements for ensuring product safety. With the implementation of the new ISO 13485:2025 standard, mold processing enterprises need to establish a quality management system covering the entire life cycle of design, manufacturing, and verification to gain a leading position in the field of medical injection molding.